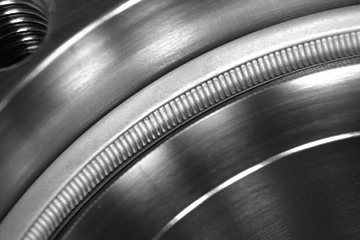
Interconnectivity Solutions
Harnessing a rich legacy of subsea expertise, our dedicated engineering team deliver pioneering subsea wet…
SubConnect provides customers with all the piece parts and equipment required to assemble jointing solutions for the installation and maintenance of fibre optic subsea cables.
The team possesses exceptional knowledge and is equipped to support our global customer base, ensuring that every individual requirement is met with great accuracy and confidence. Additionally, we offer full traceability for each part for up to 25 years.
This is achieved through a comprehensive Business Management System that complies with all ISO9001-2015 requirements. This system ensures effective management and quality control for all existing products and the development of new interconnect solutions, whether for integrating new cables into existing systems or creating innovative solutions for the evolving undersea environment.
This independent process enables SubConnect to deliver a complete 360 solution, from concept to end-of-life disposal. Unique within this sector, SubConnect possesses all necessary in-house skills, reducing the need to collaborate with external suppliers.
SubConnect have invested heavily in the management of the supply chain to ensure our suppliers are fully embedded in our processes and that they have similar inspection equipment, be these the latest optical and laser measurements system to a fully integrated ERP system to manage each stage of this complex process.
Each cable type and variant use different piece parts, whether using UJ technology or specific parts designed for a clients unique design. These parts are supplied as ‘common’ and ‘end specific’ kits, in individual, rigorously packed and protected flight cases.
Complete instructions for using the parts and assembling joints are available through the UJ & UQJ Explorer, which is available via subscription and is updated quarterly. All parts are backwards-compatible so the technology you purchase always remains current. The same level of detail is provided for each customer specific design.
In order to produce and supply high quality, fully traceable kits to our worldwide market, SubConnect has invested in a dedicated assembly, integration, test and kitting facility in excess of 15,000sqm.
Within this facility investment has been made to ensure all our kits are produced to the highest standard, from our Business Management System (ISO9001-2015 accredited) that allows complete and fully traceable records for parts and kits; these records are electronically held for a minimum of 25 years; to our extensive measurement, inspection and identification equipment.
SubConnect is the market leader in the development of fibre-based cable jointing technology and provides tools and equipment to customers around the globe, that are compatible with their specific Universal Joint and Universal Quick Joint and customer specific requirements.
There are two distinctive types of tools available, standard equipment, which can be used across all joints, identified as ‘Common Equipment’ and bespoke equipment known as ‘End Specific’. Common equipment for UJ & UQJ technology includes the jointing benches, presses and general toolkits. Because the technology for preparing each cable type is different, there is an end-specific toolkit for each cable type or interface.
The complete joint assembly will be carried out using a combination of the common tooling and the end-specific toolkits. All the toolkits are packaged in individual cases with foam cut-outs containing each tool which both offers protection and ensure that specific groups of tools remain together for easy and quick deployment when working in harsh environments.
SubConnect has built a strong foundation of expertise, skills, pioneering technology, equipment, and assets, establishing a reputation for quality, expertise, and reliability.