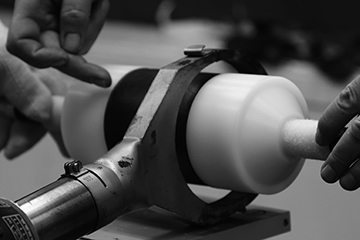
Subsea Fibre Optic Jointing
Our qualification services provide a design and qualification against international standards, ensuring that your subsea…
A cable joint is a connection between two sections of cable – specifically fibre optic cables when talking about “Universal Jointing” (UJ and/or UQJ). Universal Jointing is a technique used to connect various types of submarine optical telecommunication cables using a standardised set of jointing equipment, methods and training. The advantages of Universal Jointing (UJ/UQJ) for repairing and installing subsea fibre optic cable systems are widely recognised in the Telecommunication Industry.
As each cable varies in its manufacture and design, based upon its specific application/system requirements, for example system length or capacity – a trans-oceanic network, a regional network, a domestic festoon network or even connecting offshore oil and gas platforms – the jointing of these cables require specific and common jointing kits, tools, equipment, skill set, testing and training to ensure it meets the system requirements.
SubConnect is the leader in fibre based cable jointing technology, offering tools and equipment worldwide compatible with the Universal Joint (UJ), Universal Quick Joint (UQJ), and customer-specific needs.
We provide two types of tools: standard equipment (common across all joints) and bespoke equipment (end-specific). Common equipment for UJ and UQJ technology includes jointing benches, presses, and general toolkits. Each cable type or interface requires a unique end-specific toolkit due to varying preparation technologies.
Complete joint assembly uses a mix of common and end-specific tools. Our toolkits come in individual cases with foam cut-outs for protection and organisation, ensuring easy and quick deployment in harsh environments.
The introduction of our DXr1 camera revolutionised the inspection process for submarine cable joints after repair operations, rendering film technology obsolete.
The DXr1 generates digital radiograph images instantly, enabling immediate assessment with enhanced detail and accessibility from any location globally.
Compared to traditional film methods, this digital approach saves approximately 75% of the time typically spent. In an industry where project delays incur significant costs, sometimes tens of thousands of dollars per day due to vessel standby, such time efficiencies are indispensable. Moreover, electronically retained evaluation records and original images remove the necessity for archiving and preserving film plates.